Beyond Fasteners: Why Bond Integrity & Composite NDT Are Reshaping Aerospace Engineering
In the evolving world of aerospace manufacturing, the shift from mechanical fastening to adhesive bonding of composite structures represents more than just a design choice—it’s a leap forward in performance, fuel efficiency, and structural integrity. But as bonding replaces bolts, ensuring surface integrity before bonding becomes mission-critical. That’s where advanced nondestructive testing (NDT) steps in.
The Power of the Bond
Carbon fiber reinforced polymers (CFRPs) now form the backbone of lightweight aircraft structures, comprising 40-50% of modern aircraft by volume. Adhesive bonding offers unmatched benefits—such as weight reduction, improved fatigue performance, and elimination of stress concentrations caused by mechanical fasteners. However, even microscopic surface contaminants, like trace silicone residue from mold release agents, can silently compromise bond strength, with potential reductions of 20-70% in joint strength, leading to unpredictable failures.
Detection Demands Precision
To meet FAA certification standards and achieve reliability in bonded joints, aerospace manufacturers are turning to sophisticated surface evaluation techniques like:
- Laser-Induced Breakdown Spectroscopy (LIBS): Enables rapid, sensitive detection of contaminants at levels below 1 µg/cm²—critical for pre-bonding validation. LIBS offers exceptional sensitivity to light elements and provides detailed compositional information, though it faces challenges with shot-to-shot variations in intensity.
- Optically Stimulated Electron Emission (OSEE): Offers real-time, non-contact verification of surface cleanliness by measuring photoelectrons emitted when surfaces are exposed to ultraviolet radiation. OSEE is particularly valuable for detecting non-fluorescent contaminants like silicones that traditional black light inspection might miss.
These techniques are at the heart of research from institutions like NASA and form the foundation of process control strategies for future-ready aerospace programs. Companies like Composite Inspection and Consulting (CICNDT) are leading the way, providing specialized NDT services for assessing the integrity of aircraft composite structures throughout their operational lifespan. Their advanced bond testing techniques help identify critical issues like disbonding, delamination, and other defects within carbon fiber composites.
From Bond Integrity Lab Testing to Flight Line
The vision: inline, automated systems capable of simultaneously cleaning and characterizing composite surfaces using integrated laser ablation and LIBS sensing. This ensures bond-ready surfaces—without destructive testing, delays, or guesswork. Alternative approaches like wet blasting have also proven effective for preparing composite components by removing residues while creating consistent surfaces that maximize bond strength.
Industry leaders like Omni NDE are advancing this vision through automation expertise, developing practical and reliable systems that deliver consistent results in both controlled settings and harsh field conditions. Their collaboration with CICNDT delivers cutting-edge NDT solutions, ensuring the safety and reliability of critical components across various industries.
Innovation Hub: The AIMM Center
The Advanced Inspection and Methods and Materials (AIMM) Center in Ogden, Utah, launched in April 2025, represents the future of aerospace inspection. This cutting-edge facility is transforming aerospace NDT through cobot technology and advanced materials testing methods. Located near Hill Air Force Base in the heart of Utah’s aerospace and advanced manufacturing cluster, Ogden provides an ideal environment with a young, well-educated workforce specialized in engineering, advanced materials, manufacturing, and software development.
The AIMM Center serves as a crucial hub for collaboration between companies like CICNDT, technology providers like
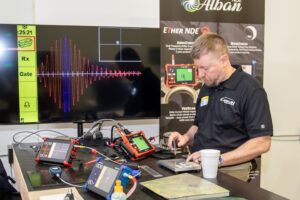
A technician performs a live non-destructive testing (NDT) demonstration focused on bond integrity using eddy current and ultrasonic inspection tools—part of the AIMM Center’s cutting-edge composite evaluation capabilities in Ogden, Utah.
, and aerospace manufacturers, accelerating the development and implementation of next-generation NDT technologies for composite structures.
Final Thought
Adhesive bonding isn’t just a structural strategy—it’s a precision science. With industry leaders establishing specific contamination testing protocols, and specialists like CICNDT delivering focused, practical, and robust non-destructive testing solutions, we’re not only building stronger bonds, we’re safeguarding the next generation of aerospace performance. These advancements enable aerospace manufacturers to fully realize the weight savings, improved assembly speeds, and enhanced design freedom that composite materials promise.